The Function of Drug Coating
Coating refers to the unit operation of applying a layer of outer coating material to the dry surface of the formulation. This coating material not only makes the product easier to identify, but even improves the pharmacokinetic properties of the drug by altering its release: ensuring that the drug reaches its target and provides sufficient concentrations in the body to be maintained for an extended period of time. Coatings are widely used in oral solid dosage forms, including tablets, capsules, multi-particulates and drug crystals. However, the most common coated dosage form is the tablet, followed by the coated multi-particulate dosage form. Reasons for using coating drug dosage forms vary, but the more common ones are: mask the unpleasant taste of APIs and excipients; improve product appearance; help manufacturers, pharmacists and patients quickly identify products; provides improved release characteristics for efficient drug release rates and ensures drug arrival at the target site; improve product stability by protecting APIs from light and moisture during storage.
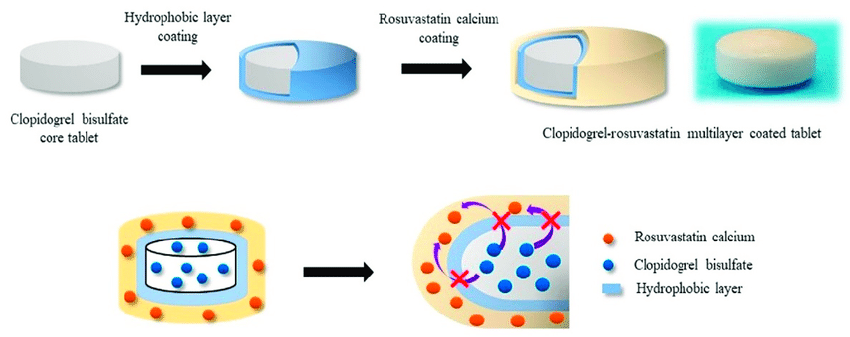
In the production of finished tablet dosage forms, film coatings are typically applied as aqueous or solvent-borne polymer systems in coating pans or fluidized beds. The function of the coating may be to improve aesthetics, provide taste masking, or modify drug release. The film coating process involves applying a thin polymer coating solution to the appropriate substrate (tablets, granules or crystals) by spray atomization techniques. To evenly distribute the coating material and prevent coating problems (fuzzing, roughness, or spotting), thin film coating parameters are optimized to create a balance between coating solution delivery rate and drying ability. Fast drying usually occurs during the coating process. Efficient air exchange ensures that there is only a short time between the impact of the coating liquid on the tablet surface and the subsequent evaporation of the solvent. Therefore, during the film coating process, the interaction between the core material and the coating liquid is usually minimal. In most cases, it is unlikely that the phase transition will occur by solution mechanisms during film coating. If desired, a polymer-based seal coat may be first applied to the surface of the tablet core prior to application of the film coat. This will prevent the expansion of solid-liquid interactions during the subsequent film coating process. Therefore, during the film coating process, the interaction between the core material and the coating liquid is usually minimal. For some extended-release products, a portion of the total dose can be used as a drug coating. Such a coating can provide immediate release in a biphasic sustained release system for rapid onset of action, or it can provide immediate release in a pulsatile delivery system. The drug layer is typically applied by spraying a drug solution or drug suspension onto the surface of the tablet, depending on drug solubility and dosage. Dissolving or suspending a drug in a liquid increases the likelihood of a phase transition via solution or solution-mediated mechanisms. When drug solutions are used for coating, there is a high probability that such manipulations will alter the solid phase of the drug, similar to what was observed during the spray drying process discussed earlier. That is, rapid solvent removal during this coating process may lead to the transformation of the drug layer into a metastable crystalline or amorphous phase via a solution mechanism. When drug suspensions are used for coating, if there is a more stable phase in the aqueous medium, there is a high probability that this manipulation will alter the solid phase of the drug through solution-mediated mechanisms.